
.png)
Good Stirling engine performance requires that a minimum free volume be maintained, i.e., the total gas volume in the working gas containment, including ducting regenerator gas heater and cooler, must be minimized. The problems of piston sealing and lubrication may present intrinsic limitations to engine life. Lubrication of both sliding pistons must be accomplished passively, or gas contamination will take place. The reciprocating power piston requires a good sliding seal to prevent effectively the passage of gas into the engine crank case. Many of the mechanical problems associated with the engine itself have been solved. Shaft thermal efficiencies up to 29% have been demonstrated at an output of 3 kw. In this system, a gas is shuttled back and forth through heat-transfer components by the displacer piston while power is extracted by the power piston.Įngine development in both the United States and the Netherlands has shown that low-power lightweight engines for possible space application are possible. Philips Laboratories in the Netherlands which involves two pistons operating in a common cylinder. Implementation of the thermodynamic cycle is difficult. Hydrogen is best, but practical reasons dictate the use of helium. Maximum performance is achieved with the lightest gases.
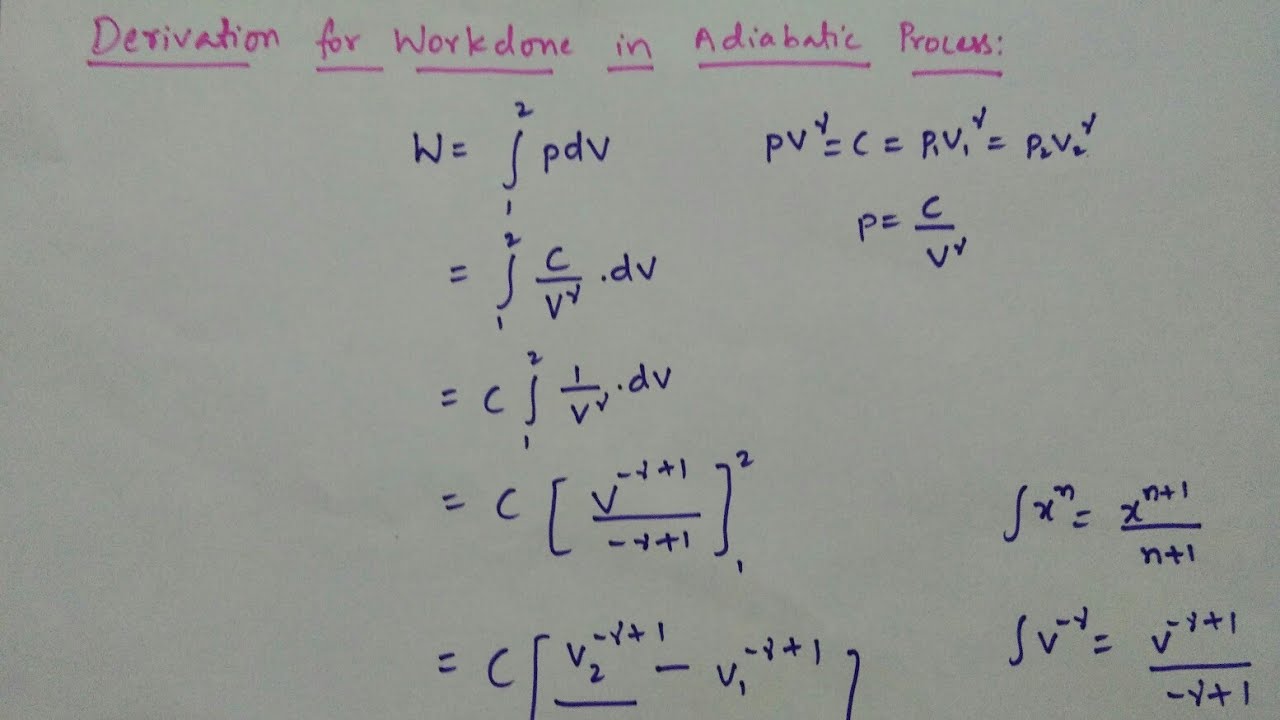
The Stirling cycle, without regeneration, is rather inefficient, but with effective regeneration, the system efficiency can be high.
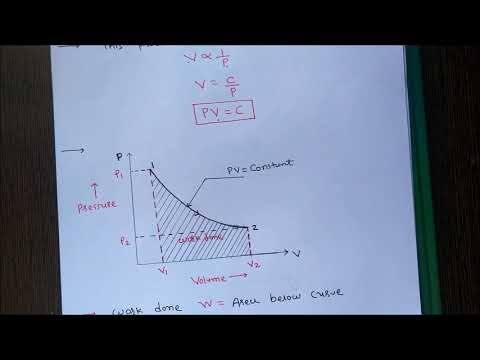
Thermodynamically, the ideal Stirling cycle consists of an isothermal compression, constant volume heat addition, isothermal expansion, and constant volume heat rejection. Streb, in Progress in Astronautics and Rocketry, 1966 Stirling Cycle While these results provided were for a CO 2 application, benefits can be realized for any high-pressure ratio application or where reducing discharge temperatures is desired (e.g., preventing ethylene polymerization).Īlan J. No reliability issues associated with the cooled diaphragm design were encountered during testing including diaphragm leakage. Additional performance gains may be realized by designing the compressor aerodynamic flow path for the cooled case rather than the adiabatic case. Operation of the cooled diaphragms changed the characteristics of the multistage machine, increasing flow capacity and pressure ratio compared to adiabatic performance at the same speed. The measured temperature drop, heat exchanger effectiveness, and power savings were all slightly higher than predicted values. The cooled diaphragms removed 297–311 K (28%–35%) of the temperature rise within each section when compared to the adiabatic case. The heat exchanger effectiveness for the cooled diaphragm was measured between 12% and 30%, depending on the stage, operating point, and back-to-back vs straight-through intercooling configurations. A 9.0% power savings was measured when the compressor was operated as a straight-through compressor with no intercooling at the design point and would be higher (> 10%) at larger flows. Additional savings would result if the machine was configured as an eight-stage compressor, which would provide two additional internal heat exchangers. Results showed that the cooled diaphragm technology reduces compressor power consumption by 3.0% near surge to 8.0% near choke when compared with the adiabatic case with intercooling between the two sections. Aerodynamic testing of the compressor in several operating configurations was completed with and without the cooling diaphragms activated. The compressor and associated piping flow loop are shown in Fig. The compressor consisted of a six-stage, back-to-back centrifugal compressor (D12R6B) that incorporated the cooled diaphragms. A new compressor was fabricated based on a Dresser-Rand DATUM D12 frame size.
